Power Electronicsand Electrical Drives
Our Engineering Servies
With our help you achieve your development goals in no time at all
With modern scientific approaches we provide innovative technology development, comprehensive simulative and measurement studies as well as advanced system studies for power electronic systems in regenerative energy or electrical drive applications. From system analysis, technology consulting or conceptual research up to simulation, prototype testing as well as introduction of series production we support you and your projects – we offer dynamic and flexible engineering services which are especially adapted to your requirements and your business.

Power Electronics and Electrical Drives
Overview and Content
Our Team
Professional Expertise, Long-term Experience and Forward-thinking Solutions
The analysis and evaluation of the operational behavior of power electronic applications and electrical drives as well as the technical design and rating of power electronic systems requires professional expertise, long-term experience and forward-thinking solutions: Together with our team that is composed of technical experts with different professional specializations with the focus on power electronic systems, electrical drives applications and renewable energy production, we meet the demands of our customers with realibilitiy, flexibility and individually adapted solutions.
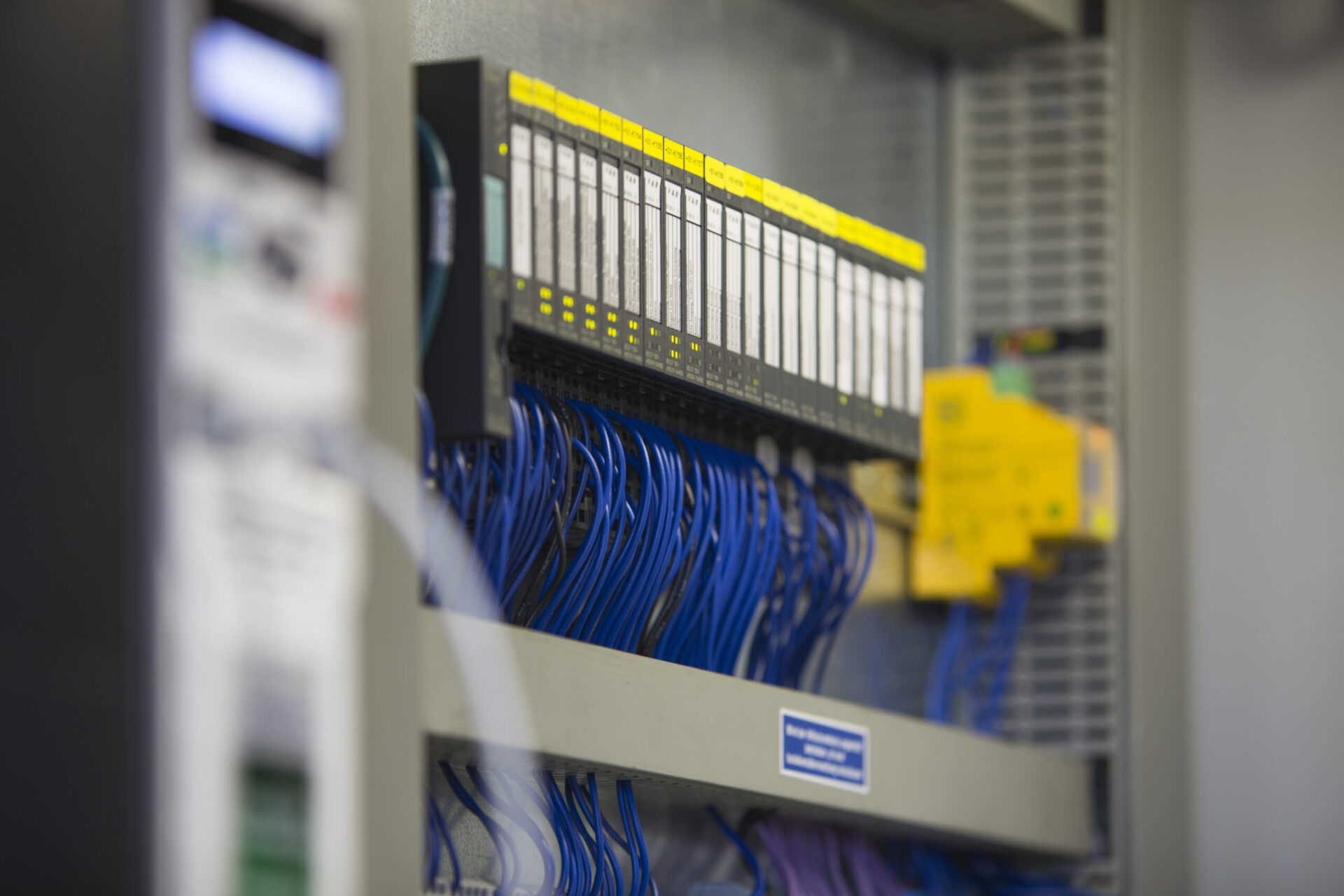
Qualification and Extensive Know-How
We develop, based on the requirements and type of the power electronic application, new and modern system concepts and become acquainted with existing systems environments without difficulties. Due to the academic basis of our team and continuous training measures with the goal of continuative professional qualification, we can support you with extensive know-how. Professional qualifications for specific industry sectors, such as safety trainings for working and rescuing at heights for wind power industry as well as general proofs of authorities such as a switching authorization for medium and high voltage systems or live working on low voltage systems under voltage, complete our expertise and facilitate effective project support with a practical orientation.
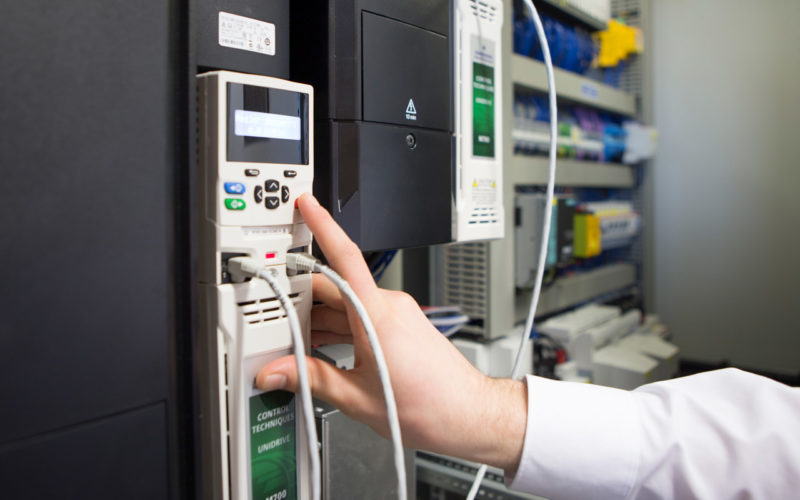
Services at a glance
Technical Design and Rating of Power Electronic System Selection of appropriate power converter circuit topologies, thermal and electrical design of passive and active components, gate drive circuits for active components, mechanical design reviews of power converters, printed circuit board design and prototyping
Analysis and Evaluation of the operational behavior of power electronic systems and electrical drives: Electrical and mechanical operating behavior, thermal operation behavior, network disturbances, power quality and electromagnetic compatibility, simulation of power electronic systems (whether offline or by means of Software-/Hardware-in-the-Loop)
Preparation of independent expert studies and reports (third party expert opinions) for government authorities, research institutes and industry companies
Technological consulting, predevelopment and professional training services for industry companies under consideration of different system concepts, feasibility studies and practical realization aspects as well as straight forward assistance in problem cases
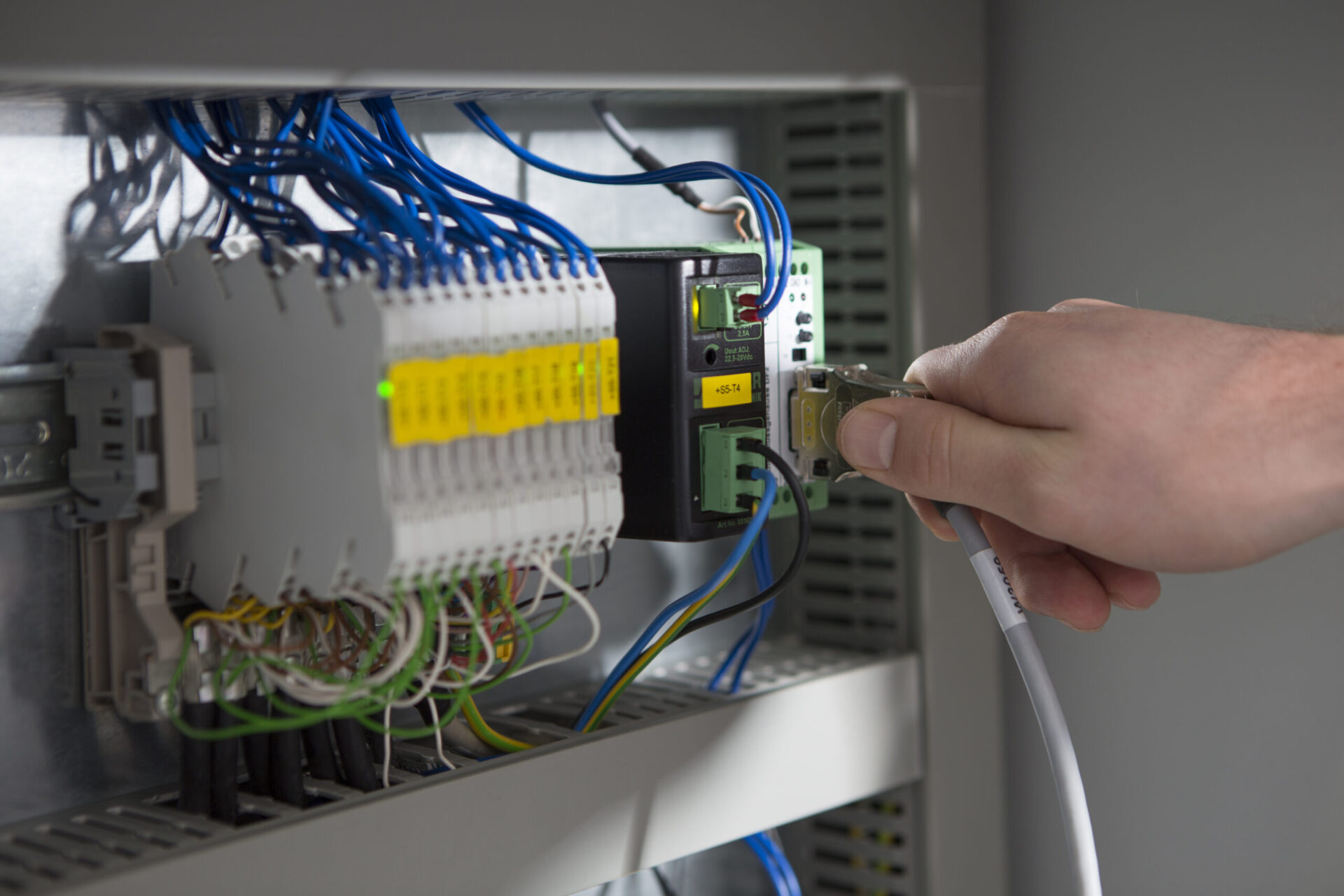
High-performance Electrical Drive Test Bench
For the analysis and optimization of adjustable-speed electrical drive systems that are fed by power electronic converters we utilize a test bench in our test laboratory. This modern and fully automated test bench allows standard-compliant testing and characterization of direct current motors, induction motors and synchronous motors either in direct grid operation or in converter-fed operation. The focus of the analysis can be placed on the frequency converter, on the electric motor or alternatively on the adjustment of both components to each other.
technical specifications
Test Bench Control
- Manual or fully automated test procedures
- Testing by means of S1 to S10 standardized load profiles or import of complex load profiles up to 2,000 supporting points
- Automatic generation of test reports or test protocols
- Database-based archiving all tests performed
Grid Connection Capacity
- 3 x 400 V / 50 Hz
- 80 A (continuous operation)
- 100 A (overload capacity)
- Network configuration: TN-C mains (IT-mains possible)
- Connectable voltage regulated variable ratio transformer (continuously adjustable from 0 to 600 V)
Load Motor
- Converter-fed and permanent-magnet synchronous motor
- Liquid-cooled with minimum load inertia
- 100 Nm nominal torque
- 300 Nm overload torque
- 2600 rpm nominal rotational speed
- 3800 rpm maximum rotational speed
- Calibrated position and rotational speed feedback
Load frequency converter
- Fully regenerative operation with controlled DC-link voltage
- 75 kW nominal power (continuous operation) motor side
- 37 kW nominal power (continuous operation) grid side
- Controlled load torque utilizing an additional torque sensor
Frequency Converter Test Device
- 4 test bays which can be chosen automatically
- Installation on partial mounting plates for fast changeover
- Complete field-bus integration for fully automated and reproducible testing
- Possibility to include additional energy storage systems (e.g. to investigate frequency converters with DC-link battery-buffer systems)
Electric Motor Test Device
- Fast mounting due to standardized flange adapters
- Mechanical mounting up to frame size (acc. to IEC 50347) 180M/L, extendable upon request
Overview about Standardized Test Methods
Parameter identification of rotating electrical machines in operation modes S1 to S10 according to IEC 60034-1
Efficiency determination for
- Direct grid connected asynchronous motors according to IEC 60034-2-1 (method 2-1-1A, method 2-1-1B, method 2-1-1C)
- Converter-fed synchronous motors according to IEC 60034-2-1 (method 2-1-2A)
- Converter-fed synchronous motors and asynchronous motors according to IEC 60034-2-3 (method 6.2)
Examples for typical test cases
Optimization of the operational behavior in relation to predetermined customer applications for converter-fed adjustable-speed drive systems
- Initial commissioning and preparation of converter parameter sets suitable for series production
- Functional validation of the drive performance
- System optimization, e.g. with respect to minimum loss operation or operation with maximum torque capability per ampere
Electrical characterization of asynchronous motors and synchronous motors
- Measurement of the rotational speed vs. torque characteristic, friction characteristic or saturation characteristic
- Identification of electrical circuit diagram parameters
- Estimation of parameter distribution for series manufactured motors
- Thermal characterization as well as determination of thermal circuit diagram parameters
Evaluation of the operational behavior of frequency converters
- Initial commissioning, field-bus integration and parametrization
- Assessment of open – and closed-loop control structures and possibilities for parameter setting in relation to predetermined customer applications or critical operation conditions
- Thermal characterization for extreme operation conditions
- Optimization of default parameter settings to achieve a improved system behavior
Modern Semiconductor- and Power Stack- Test Bench
The modern semiconductor- and power stack*- test bench in our laboratory enables the experimental determination of thermal equivalent circuit diagram parameters of power stacks as well as switching- and conduction-losses for semiconductors in power stack applications. Furthermore, the overall power stack safe-operation area can be determined and the semiconductor lifetime and thermal cycling capabilities can be estimated through extensive wear-out tests. With our professional measurement services and our fully automated test bench we support your power stack development and component tests, for example the selection and characterization of semiconductor modules or the design of gate drivers, heat sinks or DC-link capacitors.
* Power stacks are highly integrated power electronical devices. They are composed of semiconductors, a cooling system (air- or liquid-cooled) and, where required, DC-link capacitors as well as the gate-drive and safety electronics. Thus, power stacks are the core component of every modern power electronic converter.
technical specifications
Standardized Test Methods
- Thermal equivalent circuit diagram measurements:
IEC 60747-9, ed. 2.0 2007-09 (Chap. 6.3.13.1, method 1) - Switching-, conduction- and reverse recovery measurements:
IEC 60747-9, ed. 2.0 2007-09 (Chap. 6.3.11 and 6.3.13)
Test Bench Controls
- Fully automated test bench control is realised by an PLC
- Target: high degree of test automatization and test reproducibility
- Target platform: Beckhoff embedded industrial PC with TwinCAT3 I/O module periphery
- Supported field bus systems: Ethercat, Profinet IO RT
Forced Air Cooling
- Speed controlled-fan air cooling
- Temperature range of the test chamber: 25°C – 55°C
- Ambient temperature range: 20°C – 35°C
Liquid Cooling System
- Air liquid heat exchanger
- Temperature range of the cooling liquid: 10°C – 70°C
- Ambient temperature: 20°C – 30°C
- Flow rate range (regulated): 10 – 65 l/min
- Heating capacity: 3 kW, Cooling capacity: 6 kW
Overview of the Test Bench Interfaces to Device Under Test
Device Under Test (DUT) Power Supply
- 0 – 80 V, 1500 A (45 kW) high current source (pole-reversible) for thermal characterisation
- 0 – 2000 V, 2 A (4 kW) high voltage source for switching characterisation
- 400 V/230 V (L1/L2/L3/N/PE) 16A for DUT AC auxiliary power supply
- 24 V, 5 A / +15 V, 7 A / -15 V, 4 A / 5 V, 7 A for DUT DC auxiliary power supply
Control Interfaces
- General control: 8 digital outputs (potential free)
- IGBT control monitoring: 12 digital outputs (15 / 24 V, 1 MS/s)
- supported thermocouples types K, J, L, E, T, N, U, B, R, S, C (24 analogue inputs)
- RTD- and NTC-temperature measurement (8 analogue inputs)
Innovative Back-to-Back Test Bench
Modern wind turbine systems are using frequency converters frequency adjustment between the variable-frequency generator and the fixed-frequency supply network. The advanced back-to-back test bench in our test laboratory is used for the optimization of frequency converters in modern wind turbines – for example, by increasing the power density per wind turbine. With our test bench it is possible, among other things, to test frequency converters up to 1.400 V without further restrictions. In addition, the use of an additional frequency converter at the grid connection point of the test bench allows to emulate the behavior of a typical generator of a modern wind turbine.
technical specifications
Overall test bench specification
- Nominal current: 6.000 Arms
- Nominal voltage: 400 – 1.400 Vrms (adjustable)
- Nominal apparent power: 7,5 MVA
- Nominal looses: 400 kVA (overall)
- Power factor: -1 … 0 … 1 (adjustable)
- Frequency: 10 … 500 Hz (adjustable)
- DUT Converter types: two-level and three-level voltage source converters
- DUT carrier frequency: 150 Hz … 15 kHz (adjustable)
Test bench highlights at the glance
- Ready for 1.400 V ac
- Capable of full apparent power of freuqnecy converters with individual controlled active and reactive power
- Measurement under dynamic load conditions, e.g. transient overloads conditions or FRT performance
Customized based upon your Needs
Advanced Training and Workshops
We offer advanced training services with the focus on power electronics, electrical drives and renewable energy technologies. Our team consists of academically qualified development engineers exclusively. We plan seminars and create contents to individually meet the customers needs. Contents range from basic technical concepts up to special applications based on the customers´ wishes. Training services are available as on-site in-house training, via video- or conference call our in our facilities in Halle/Peißen. Our advanced training and workshop services can be held in small groups of participants as well as in front of a large audience. With pleasure we provide you an individual offer. Please do not hesitate to contact us for any questions or further information.
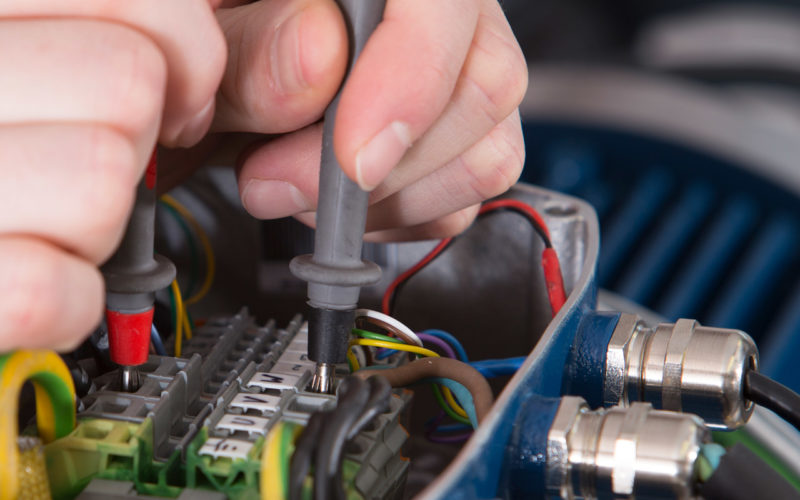
Workshop-Themen
From the Idea to the Prototype
3D Construction of Components
Modern 3D construction has become a central component of prototype development in power electronics and electric drive technology. With our 3D construction service in CAD design, power stacks and related components of power electronics can be designed. We work on the basis of established standards and relevant design features of mechanics and electrical engineering, taking into account the coordination of insulation (e.g. after DIN EN-61800-5-1 oder nach IEC 61287). The subsequent production of the prototypes and the associated type test can be carried out in our laboratories.
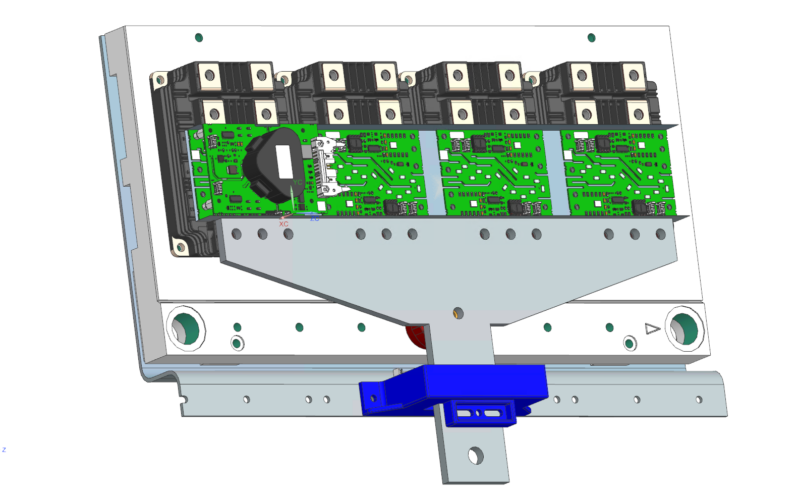
Thermal Simulation
Thermal Characterization of Semiconductors
The simulation of thermal behavior is an important part of the product development of temperature-sensitive components in power electronics and electrical drive technology. With our modern semiconductor- and power stack-test bench, thermal equivalent circuit diagrams of power stacks as well as switching and conduction losses of power semiconductors in power stacks can be determined. With the help of these thermal equivalent circuit diagrams, virtual power stacks are created and load profiles are thermally simulated. Parameters such as ambient temperature, switching frequency and switching pattern can be set variably here and systems can be designed up to the thermal limits inherent in the system.
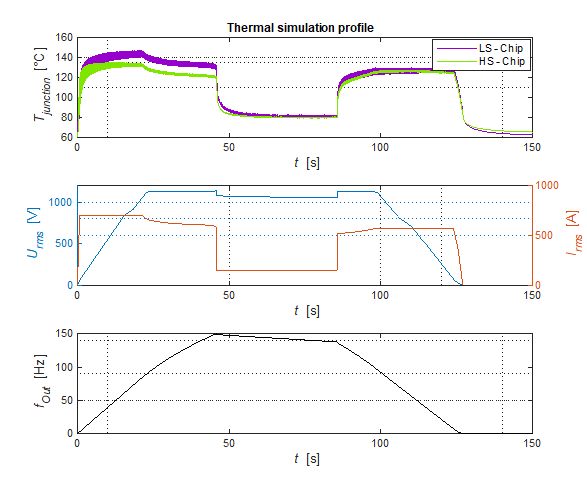
Lifetime Calculation of Converters
Service Life of various Drive Applications
The service life of converters for different drive applications can vary depending on the load and is of central importance for the planning and design of wind or load drives. The basis for calculating the service life of a converter is the load profile as a torque/speed profile or a profile with converter currents and voltages. In addition, thermal impedances and switching energies of the converters are taken into account in order to calculate the losses and the temperatures of the components for a load profile. The temperature cycles are evaluated using a standard rainflow with a rainflow algorithm optimized by post-processing.
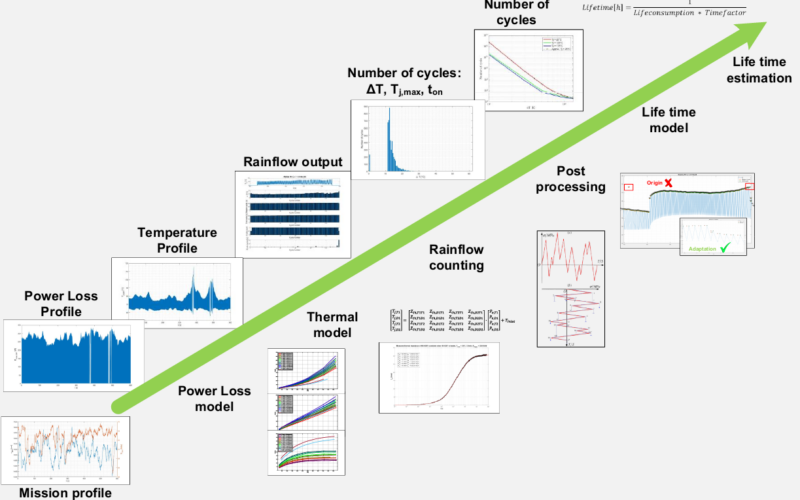
Head of R&D department Dr.-Ing Nils Hoffmann
Nils Hoffmann studied electrical engineering and received the Dipl.-Ing. and Dr.-Ing. degrees from the Christian-Albrechts-University of Kiel, Kiel, Germany, in 2009 and 2014, respectively. Between 2009 and 2013, he was with the Institute of Power Electronics and Electrical Drives, Christian-Albrechts-University of Kiel, where he was involved in modern control strategies applied to grid-connected power converter systems. Since 2013, he has been with the Ingenieurbüro Hoffmann GmbH, Halle/Saale, Germany, where he is the Head of Research and Product Development for Power Electronics and Electrical Drives. He is involved in modern and innovative concepts of power electronic systems, electrical drives and renewable energy applications with the focus on technological consulting, assistance in problem cases, feasibility studies, preliminary and ready-to-release system designs, prototyping, and fundamental and advanced training services. His current research interests include the control of power converters and drives, power quality in distributed power generation networks, and modern multilevel converter topologies for high power adjustable speed drive applications.
Resume and cornerstones
Nils Hoffmann presented his research results regularly on international accepted conferences such as IEEE Energy Conversion Congress and Exposition where his oral presentations have been recognized with the IEEE ECCE Student Presentation Awards in 2011 and 2012. As an active member of IEEE Industrial Electronics Society, IEEE Industry Applications Society, IEEE Power Electronics Society and VDE Power Engineering Society, Nils Hoffmann is remaining familiar with the latest research results and developments, even after his academic career. His reputation as an technical expert in the field for power electronic application is confirmed for example by the intense requests to work as an scientific reviewer for international and peer-reviewed journals such as IEEE Transactions on Power Electronics, IEEE Transactions on Industrial Electronics, IEEE Transactions on Industry Applications, IEEE Journal of Emerging an Selected Topics in Power Electronics, IEEE Transactions on Industrial Informatics and the IET Journal on Power Electronics.
In October 2014 Nils Hoffmann received the VDE/ETG best paper award as a recognition for his outstanding scientific work and publicistic contributions form the German VDE Power Engineering Society. Also in 2014, Nils Hoffmann received the Dr.-Ing. degree with honors form the Christian-Albrechts-University of Kiel for his PhD-thesis entitled “Grid-adaptive control and active-filter functionality of grid-connected PWM converters in renewable energy generation”. Examiners of the PhD thesis were Prof. Dr. F. W. Fuchs (Christian-Albrechts-University of Kiel, Germany), Prof. Dr. F. Blaabjerg (Aalborg University, Denmark) and Prof. Dr. M. P. Kazmierkowski (Warsaw University of Technology, Poland).
In addition to his scientific research, Nils Hoffmann is focusing on technology transfer to industrial partners. The application and product-oriented scientific research was carried out in collaboration with industrial partners such as Danfoss Solar Inverters A/S, Danfoss Drives A/S, Danfoss High-Power-Converters Inc., kk-electronic A/S and Converteam GmbH (today: GE Energy Power Conversion GmbH). The numerous cooperation with industrial partners in predevelopment and technological consulting show the high relevance of his research results for practical applications.
Complete list of publications
Hoffmann, L. Asiminoaei, S. Hansen and F. W. Fuchs, “Shunt active filter with optimum reference generation algorithm for power factor and harmonic current compensation”, Proc. of IEEE Energy Conversion Congr. and Exposition, pp. 2784-2793, Sept. 2009.
Hoffmann, S. Thomsen and F. W. Fuchs, “Model based predictive speed control of a drive system with torsional loads – A practical approach”, Proc. of 14th Int. Power Electron. and Motion Control Conf., pp. T5-149, Sept. 2010.
Hoffmann, S. Thomsen and F. W. Fuchs, “Appropriate tuning and robust design of a generalized predictive speed controller for drive systems with resonant loads”, Proc. of IEEE Energy Conversion Congr. and Exposition, pp. 764-771, Sept. 2010.
Hoffmann, F. W. Fuchs and J. Dannehl, “Models and effects of different updating and sampling concepts to the control of grid-connected PWM converters – A study based on discrete time domain analysis”, Proc. of 14th Eur. Conf. on Power Electron. and Appl., pp. 1-10, Aug. 2011.
N. Hoffmann, R. Lohde, M. Fischer, F. W. Fuchs, L. Asiminoaei and P. B. Thøgersen, “A review on fundamental grid-voltage detection methods under highly distorted conditions in distributed power-generation networks”, of IEEE Energy Conversion Congr. and Exposition, pp. 3045-3052, Sept. 2011.
Hoffmann, F. W. Fuchs and L. Asiminoaei, “Online grid-adaptive control and active-filter functionality of PWM-converters to mitigate voltage-unbalances and voltage-harmonics – a control concept based on grid-impedance measurement”, Proc. of IEEE Energy Conversion Congr. and Exposition, pp. 3067-3074, Sept. 2011.
Hoffmann, M. Hempel, M.C. Harke and F.W. Fuchs, “Observer-based Grid Voltage Disturbance Rejection for Grid Connected Voltage Source PWM Con-verters with Line Side LCL filters”, Proc. of IEEE Energy Conversion Congr. and Exposition, pp. 69-76, Sept. 2012.
Hoffmann and F.W. Fuchs, “Online Grid Impedance Estimation for the Control of Grid Connected Converters in Inductive-Resistive Distributed Power-Networks Using Extended Kalman-Filter”, Proc. of IEEE Energy Conversion Congr. and Exposition, pp. 922-929, Sept. 2012.
Hoffmann, M. Andresen, L. Asiminoaei, F.W. Fuchs and P. B. Thøgersen, “Variable Sampling Time Finite Control-Set Model Predictive Current Control for Voltage Source Inverters”, Proc. of IEEE Energy Conversion Congr. and Exposition, pp. 2215-2222, Sept. 2012.
Thomsen, N. Hoffmann and F. W. Fuchs, “Comparative study of conventional PI-control, PI-based state space control and model based predictive control for drive systems with elastic coupling”, Proc. of IEEE Energy Conversion Congr. and Exposition, pp. 2827-2835, Sept. 2010.
Wessels, N. Hoffmann and F. W. Fuchs, “Regelung der negativen Spannungssequenz durch Windenergieanlagen – Negative sequence voltage control for wind turbines”, Internationaler ETG-Kongress, vol. ETG-FB 130, Nov. 2011.
W. Fuchs, N. Hoffmann, J. Reese, C. Wessels, R. Lohde, S. Grunau and F. Gebhardt, “Research Laboratory for Grid-integration of Distributed Renewable Energy Resources – Integration Analysis of DERs -” Prof. of 14th Int. Power Electron. and Motion Control Conf., pp. 1-10, Sept. 2012.
W. Fuchs, F. Gebhardt, N. Hoffmann, A. Knop, R. Lohde, J. Reese and C. Wessels, “Research Laboratory for Grid-integration of Distributed Renewable Energy Resources – Design and Realization -” Proc. of IEEE Energy Conversion Congr. and Exposition, pp. 1974-1981, 15-20 Sept. 2012.
Hoffmann and F. W. Fuchs, “Minimal Invasive Equivalent Grid Impedance Estimation in Inductive-Resistive Power-Networks using Extended Kalman-Filter”, IEEE Trans. Power Electron., vol. 29, no. 2, pp. 631-641, Feb. 2014.
Thomsen, N. Hoffmann and F. W. Fuchs, “PI Control, PI-Based State Space Control, and Model-Based Predictive Control for Drive Systems With Elastically Coupled Loads – A Comparative Study”, IEEE Trans. Ind. Electron., vol. 58, no. 8, pp. 3647-3657, Aug. 2011.
Wessels, N. Hoffmann, M. Molinas and F. W. Fuchs, “StatCom Control at Wind Farms with Fixed Speed Induction Generators under Asymmetrical Grid Faults”, IEEE Trans. Ind. Electron., vol. 60, no. 7, pp. 2864-2873, July 2013.
Panten, N. Hoffmann, N. and F. Fuchs, , “Finite Control Set Model Predictive Current Control for Grid-Connected Voltage-Source Converters with LCL-Filters: A study based on different State Feedbacks,” IEEE Trans. Power Electron., vol. 31, no. 7, pp. 5189-5200, 2016.
Hoffmann, F.W. Fuchs, M.P. Kazmierkowski, and D. Schröder, “Digital current control in a rotating reference frame Part I: System modeling and the discrete time-domain current controller with improved decoupling capabilities,” IEEE Trans. Power Electron., vol. 31, no. 7, pp.5290-5305, 2016.
Hoffmann, F. W. Fuchs und D. Schröder, “Indirekte Stromregelverfahren für Drehfeldmaschinen” (Kapitelbeitrag) Elektrische Antriebe – Regelung von Antriebssystemen, 4. Auflage, Springer, ISBN 978-3-642-30095-0, 2015.
Hoffmann, “Grid-adaptive control and active-filter functionality of grid-connected PWM converters in renewable energy generation”, Dissertation, available online, urn:nbn:de:gbv:8-diss-163567, 2015.